Ball bearing sizes and dimensions vary based on the type and application. They are typically measured by inner diameter (ID), outer diameter (OD), and width (W) in millimeters or inches. Standard sizes follow ISO and ANSI standards.
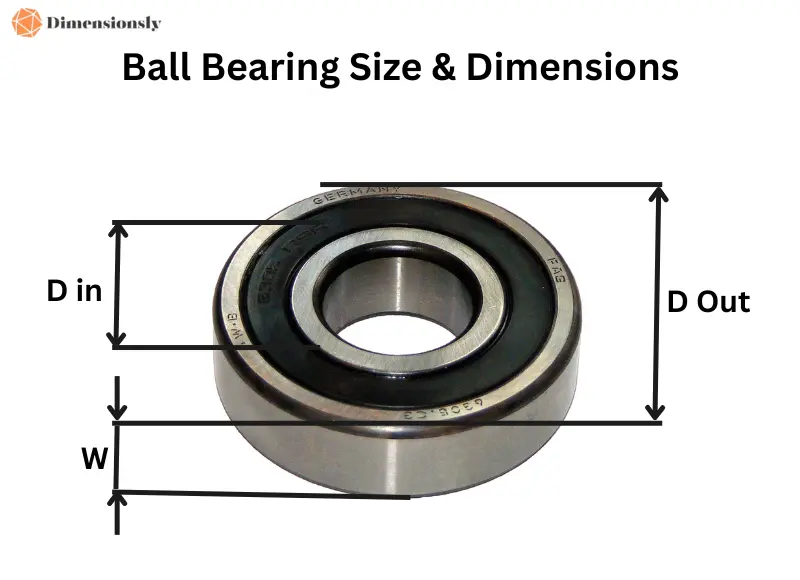
Ball Bearing Sizes and Dimensions
6000 Series Ball Bearing Sizes
Size | Inner Dimension (mm) | Outer Dimension (mm) | Width (mm) | Dynamic (Cr) | Static (Cor) | Weight (lb) |
---|---|---|---|---|---|---|
6000 | 10 | 26 | 8 | 1030 | 445 | 0.042 |
6001 | 12 | 28 | 8 | 1147 | 535 | 0.048 |
6002 | 15 | 32 | 9 | 1254 | 641 | 0.068 |
6003 | 17 | 35 | 10 | 1349 | 731 | 0.088 |
6004 | 20 | 42 | 12 | 2109 | 1129 | 0.150 |
6005 | 25 | 47 | 12 | 2248 | 1315 | 0.172 |
6006 | 30 | 55 | 13 | 2967 | 1866 | 0.242 |
6007 | 35 | 62 | 14 | 3642 | 2360 | 0.0326 |
6008 | 40 | 68 | 15 | 3867 | 2653 | 0.407 |
6009 | 45 | 75 | 16 | 4721 | 3327 | 0.506 |
6010 | 50 | 80 | 16 | 4946 | 3642 | .0568 |
6011 | 55 | 90 | 18 | 6789 | 4901 | .0796 |
6012 | 60 | 95 | 18 | 7081 | 5440 | .0847 |
6013 | 65 | 100 | 18 | 6857 | 5665 | 0.957 |
6014 | 70 | 110 | 20 | 8565 | 6947 | 1.324 |
6015 | 75 | 115 | 20 | 8902 | 7531 | 1.404 |
6016 | 80 | 125 | 22 | 10701 | 8947 | 1.870 |
6017 | 85 | 130 | 22 | 11128 | 9689 | 1.958 |
6018 | 90 | 140 | 24 | 13084 | 11173 | 2.552 |
6019 | 95 | 145 | 24 | 13578 | 12117 | 2.662 |
6020 | 100 | 150 | 24 | 13533 | 12185 | 2.750 |
6021 | 105 | 160 | 26 | 16254 | 14792 | 3.498 |
6022 | 110 | 170 | 28 | 18434 | 16411 | 4.312 |
6024 | 120 | 180 | 28 | 18659 | 17535 | 4.796 |
6026 | 130 | 200 | 33 | 23380 | 22481 | 7.326 |
6028 | 140 | 210 | 33 | 24279 | 24279 | 7.832 |
6030 | 150 | 225 | 35 | 27427 | 28101 | 9.636 |
6200 Series
Size | Inner Dimension (mm) | Outer Dimension (mm) | Width (mm) | Dynamic (Cr) | Static (Cor) | Weight (lb) |
---|---|---|---|---|---|---|
6200 | 10 | 30 | 9 | 1147 | 535 | 0.070 |
6201 | 12 | 32 | 10 | 1533 | 686 | 0.077 |
6202 | 15 | 35 | 11 | 1720 | 836 | 0.099 |
6203 | 17 | 40 | 12 | 2154 | 1075 | 0.141 |
6204 | 20 | 47 | 14 | 2878 | 1495 | 0.227 |
6205 | 47 | 52 | 15 | 3147 | 1771 | 0.279 |
6206 | 30 | 62 | 16 | 4384 | 2585 | 0.440 |
6207 | 35 | 72 | 17 | 5733 | 3417 | 0.634 |
6208 | 40 | 80 | 15 | 6632 | 4047 | 0.810 |
6209 | 45 | 85 | 19 | 7081 | 4609 | 0.915 |
6210 | 50 | 90 | 20 | 7868 | 5216 | 1.019 |
6211 | 55 | 100 | 21 | 9757 | 6609 | 1.335 |
6212 | 60 | 110 | 22 | 11780 | 8138 | 1.723 |
6213 | 65 | 120 | 23 | 12859 | 9015 | 2.178 |
6214 | 70 | 125 | 24 | 13983 | 9914 | 2.354 |
6215 | 75 | 130 | 25 | 15152 | 10858 | 2.596 |
6216 | 80 | 140 | 26 | 16344 | 11915 | 3.080 |
6217 | 85 | 150 | 28 | 18884 | 13916 | 3.938 |
6218 | 90 | 160 | 30 | 21604 | 16074 | 4.730 |
6219 | 95 | 170 | 32 | 24504 | 18412 | 5.764 |
6220 | 100 | 180 | 34 | 27427 | 20930 | 6.908 |
6221 | 105 | 190 | 36 | 29899 | 23605 | 8.140 |
6222 | 110 | 200 | 38 | 32372 | 26303 | 9.592 |
6224 | 120 | 215 | 40 | 32822 | 27427 | 12.386 |
6226 | 130 | 230 | 40 | 37318 | 32822 | 13.728 |
6228 | 140 | 250 | 42 | 39566 | 37318 | 17.754 |
6230 | 150 | 270 | 45 | 39566 | 38217 | 22.660 |
6300 Series
Size | Inner Dimension (mm) | Outer Dimension (mm) | Width (mm) | Dynamic (Cr) | Static (Cor) | Weight (lb) |
---|---|---|---|---|---|---|
6300 | 10 | 35 | 11 | 1720 | 782 | 0.12 |
6301 | 12 | 37 | 12 | 2185 | 1142 | 0.13 |
6302 | 15 | 42 | 13 | 2585 | 1218 | 0.18 |
6303 | 17 | 47 | 14 | 3035 | 1479 | 0.24 |
6304 | 20 | 52 | 15 | 3552 | 1771 | 0.31 |
6305 | 25 | 62 | 17 | 4991 | 2585 | 0.48 |
6306 | 30 | 72 | 19 | 6070 | 3417 | 0.77 |
6307 | 35 | 80 | 21 | 7464 | 4316 | 1.00 |
6308 | 40 | 90 | 23 | 9172 | 5395 | 1.41 |
6309 | 45 | 100 | 25 | 11870 | 7149 | 1.92 |
6310 | 50 | 110 | 27 | 13938 | 8610 | 2.35 |
6311 | 55 | 120 | 29 | 16096 | 10116 | 3.01 |
6312 | 60 | 130 | 31 | 18412 | 11735 | 3.74 |
6313 | 65 | 140 | 33 | 20840 | 13466 | 4.58 |
6314 | 70 | 150 | 35 | 23380 | 15322 | 5.54 |
6315 | 75 | 160 | 37 | 25403 | 17355 | 6.64 |
6316 | 80 | 170 | 39 | 27651 | 19491 | 7.90 |
6317 | 85 | 180 | 41 | 29899 | 21761 | 9.31 |
6318 | 90 | 190 | 43 | 32148 | 24054 | 10.80 |
6319 | 95 | 200 | 45 | 34396 | 26752 | 12.47 |
6320 | 100 | 215 | 47 | 38892 | 31698 | 15.40 |
6321 | 105 | 225 | 49 | 41365 | 34396 | 17.71 |
6322 | 110 | 240 | 50 | 46086 | 40465 | 20.99 |
6324 | 120 | 260 | 55 | 47659 | 42714 | 28.16 |
6326 | 130 | 280 | 58 | 51256 | 48559 | 40.26 |
6328 | 140 | 300 | 62 | 57326 | 55078 | 49.06 |
6330 | 150 | 320 | 65 | 64070 | 67442 | 58.74 |
6700 Series
Size | Inner Dimension (mm) | Outer Dimension (mm) | Width (mm) | Dynamic (Cr) | Static (Cor) | Weight (lb) |
---|---|---|---|---|---|---|
6701 | 12 | 18 | 4 | 205 | 119 | 0.004 |
6702 | 15 | 21 | 4 | 191 | 110 | 0.005 |
6703 | 17 | 23 | 4 | 216 | 137 | 0.006 |
6704 | 20 | 27 | 4 | 232 | 162 | 0.010 |
6705 | 25 | 32 | 4 | 246 | 187 | 0.015 |
6706 | 30 | 37 | 4 | 263 | 220 | 0.018 |
6707 | 35 | 44 | 5 | 416 | 366 | 0.021 |
6800 Series
Size | Inner Dimension (mm) | Outer Dimension (mm) | Width (mm) | Dynamic (Cr) | Static (Cor) | Weight (lb) |
---|---|---|---|---|---|---|
6800 | 10 | 19 | 5 | 411 | 208 | 0.011 |
6801 | 12 | 21 | 5 | 432 | 234 | 0.0132 |
6802 | 15 | 24 | 5 | 468 | 286 | 0.0154 |
6803 | 17 | 26 | 5 | 632 | 387 | 0.0176 |
6804 | 20 | 32 | 7 | 899 | 555 | 0.0418 |
6805 | 47 | 37 | 7 | 967 | 663 | 0.0484 |
6806 | 30 | 42 | 7 | 1057 | 821 | 0.0572 |
6807 | 35 | 47 | 7 | 1102 | 910 | 0.0638 |
6808 | 40 | 52 | 7 | 1113 | 944 | 0.0726 |
6809 | 45 | 58 | 7 | 1394 | 1214 | 0.088 |
6810 | 50 | 65 | 7 | 1484 | 1371 | 0.1144 |
6811 | 55 | 72 | 9 | 1978 | 1821 | 0.1826 |
6812 | 60 | 78 | 10 | 2585 | 2383 | 0.2288 |
6813 | 65 | 85 | 10 | 2675 | 2585 | 0.2772 |
6814 | 70 | 90 | 10 | 2720 | 2675 | 0.2948 |
6815 | 75 | 95 | 10 | 2810 | 2900 | 0.3124 |
6816 | 80 | 100 | 10 | 2855 | 2990 | 0.33 |
6817 | 85 | 110 | 13 | 4204 | 4271 | 0.5852 |
6818 | 90 | 115 | 13 | 4271 | 4429 | 0.6138 |
6819 | 95 | 120 | 13 | 4339 | 4429 | 1.551 |
6820 | 100 | 125 | 13 | 4406 | 4766 | 0.6798 |
6821 | 105 | 130 | 13 | 4451 | 5373 | 0.7128 |
6822 | 110 | 140 | 16 | 6317 | 6902 | 1.3332 |
6824 | 120 | 150 | 16 | 6519 | 7419 | 1.441 |
6826 | 130 | 165 | 18 | 8295 | 9262 | 2.0658 |
6828 | 140 | 175 | 18 | 8588 | 9981 | 2.2 |
6830 | 150 | 190 | 20 | 10746 | 12342 | 3.08 |
6900 Series
Size | Inner Dimension (mm) | Outer Dimension (mm) | Width (mm) | Dynamic (Cr) | Static (Cor) | Weight (lb) |
---|---|---|---|---|---|---|
6900 | 10 | 22 | 6 | 652 | 326 | 0.010 |
6901 | 12 | 24 | 6 | 967 | 506 | 0.011 |
6902 | 15 | 28 | 7 | 1034 | 573 | 0.017 |
6903 | 17 | 30 | 7 | 1428 | 832 | 0.018 |
6904 | 20 | 37 | 9 | 1574 | 1023 | 0.036 |
6905 | 47 | 42 | 9 | 1630 | 1124 | 0.041 |
6906 | 30 | 47 | 9 | 2450 | 1742 | 0.045 |
6907 | 35 | 55 | 10 | 3080 | 2237 | 0.073 |
6908 | 40 | 62 | 12 | 3170 | 2450 | 0.112 |
6909 | 45 | 68 | 12 | 3260 | 2630 | 0.132 |
6910 | 50 | 72 | 12 | 3732 | 3170 | 0.133 |
6911 | 55 | 80 | 13 | 4541 | 3889 | 0.185 |
6912 | 60 | 85 | 13 | 3912 | 3619 | 0.104 |
6913 | 65 | 90 | 13 | 5328 | 4766 | 0.211 |
6914 | 70 | 100 | 16 | 5485 | 5081 | 0.342 |
6915 | 75 | 105 | 16 | 5620 | 5395 | 0.363 |
6916 | 80 | 110 | 16 | 7171 | 6654 | 0.382 |
6917 | 85 | 120 | 18 | 7374 | 7104 | 0.535 |
6918 | 90 | 125 | 18 | 7576 | 7531 | 0.565 |
6919 | 95 | 130 | 18 | 10116 | 9419 | 0.705 |
6920 | 100 | 140 | 20 | 10454 | 10071 | 0.960 |
6921 | 105 | 145 | 20 | 10768 | 10746 | 1.000 |
6922 | 110 | 150 | 20 | 12859 | 12792 | 1.040 |
6924 | 120 | 165 | 22 | 15647 | 15737 | 1.410 |
6926 | 130 | 180 | 24 | 16029 | 16816 | 1.860 |
6928 | 140 | 190 | 24 | 20997 | 21199 | 1.980 |
6930 | 150 | 210 | 28 | 21000 | 326 | 3.050 |
Understanding Ball Bearing Sizes
Ball bearings come in various sizes, each optimized for specific load capacities and speed requirements. The right size ensures smooth operation, reduces friction, and extends the lifespan of machinery.
However, selecting the ideal size involves trade-offs. Larger bearings support heavier loads but generate more friction, limiting rotational speed. Conversely, smaller bearings enable higher speeds but may wear out faster under heavy loads.
Engineers must also consider environmental factors such as temperature, lubrication, and contamination. High-speed applications, like electric motors, require smaller, precision bearings, whereas heavy-duty machinery demands larger, more durable options.
Space constraints add another challenge—while compact designs favor smaller bearings, longevity may be compromised. Balancing these factors is crucial. The wrong size can lead to equipment failure, increased maintenance costs, and inefficiencies.
By carefully evaluating load, speed, and environmental conditions, engineers can optimize performance and reliability, ensuring the right bearing for every application.
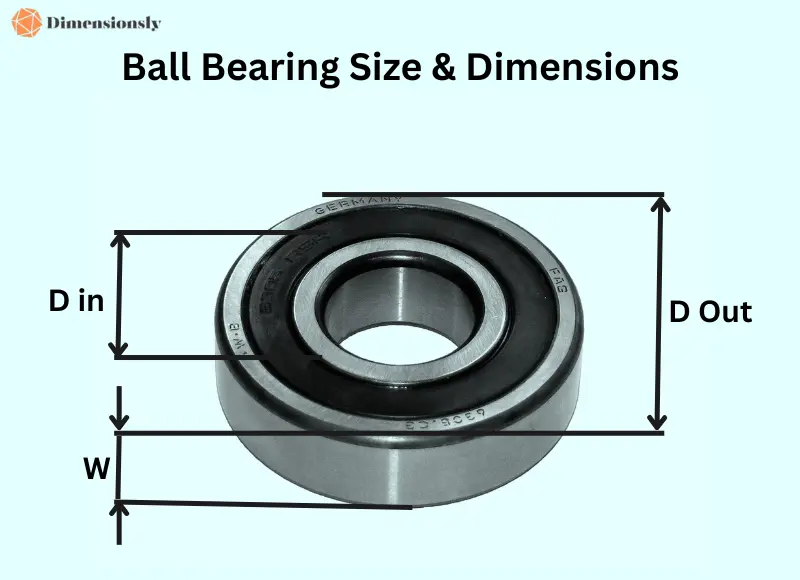
Standard Bearing Dimensions and Measurements
Bearings are measured using a standard set of dimensions: inner diameter (ID), outer diameter (OD), and width (W). These measurements determine how well a bearing fits within a system and directly impact performance.
Selecting the correct dimensions is essential because even a small mismatch can lead to misalignment, excessive wear, or system failure. One of the biggest trade-offs in choosing bearing dimensions is balancing size and load capacity.
Larger bearings support heavier loads but require more space and may add weight to the system. Meanwhile, smaller bearings save space and reduce friction, yet they may not withstand high loads or prolonged stress.
Engineers must also consider operating conditions like temperature, lubrication, and speed limits to prevent premature wear. Ignoring these factors can lead to inefficiencies, costly breakdowns, and reduced equipment lifespan. By carefully evaluating dimensions based on application needs, engineers can ensure optimal performance and reliability.
ISO and ANSI Standards for Bearings
To ensure global compatibility, ball bearings follow international standards set by ISO (International Organization for Standardization) and ANSI (American National Standards Institute). These standards define key specifications, including dimensions, load capacities, material properties, and performance tolerances.
Adhering to these guidelines ensures consistency, reliability, and interchangeability across industries. However, balancing standardization with specific application needs presents challenges. While standardized bearings simplify sourcing and reduce costs, some industries require specialized designs.
For example, high-speed aerospace applications demand ultra-precise tolerances, while heavy-duty industrial machinery prioritizes load capacity. Engineers must decide whether to use standard bearings for affordability and availability or invest in custom bearings for optimized performance.
Ignoring these standards can lead to mechanical failures, compatibility issues, and increased maintenance costs. By carefully evaluating factors like speed, load, and environmental conditions, engineers can select the right bearing standard. This ensures maximum efficiency, durability, and seamless integration into their systems.
How to Read Bearing Codes and Markings
Each ball bearing has a unique identification code that provides information about its size, type, and special features. These markings help engineers and buyers select the right bearing for their application by indicating dimensions, load capacity, precision level, and material composition.
Understanding these codes ensures compatibility and prevents costly installation errors. However, decoding bearing markings can be challenging, as different manufacturers may use variations in numbering systems.
While standardized codes, such as those defined by ISO and ANSI, simplify identification, some specialized bearings include extra suffixes and prefixes that specify unique properties like high-speed capability, corrosion resistance, or special lubrication.
Engineers must balance the trade-off between using readily available standard bearings and investing in specialized ones tailored to specific operational demands. Misinterpreting these markings can lead to performance inefficiencies, premature wear, or mechanical failures.
By carefully analyzing bearing codes, considering application requirements, and consulting manufacturer guidelines, engineers can make informed decisions that optimize performance, reliability, and longevity.
Choosing the Right Bearing Size for Your Application
Selecting the right ball bearing size depends on several key factors, including load capacity, speed, and environmental conditions. Balancing these elements is essential for ensuring optimal performance and longevity.
For instance, high-load applications require larger bearings to distribute weight evenly, whereas high-speed operations demand smaller bearings to reduce friction and maintain velocity. One of the challenges engineers face is finding the right trade-off between load-bearing capacity and speed.
While larger bearings support heavier loads, they also generate more heat, which can reduce efficiency and increase wear. Conversely, smaller bearings excel at high speeds but may not handle excessive loads without compromising lifespan.
Environmental factors, such as temperature, moisture, and exposure to chemicals, also play a significant role. Bearings used in harsh environments, like in automotive or industrial machinery, often need special coatings or materials to prevent corrosion and wear.
Carefully evaluating all these factors ensures that engineers select the optimal bearing size for their specific application. Misjudging these factors can lead to performance issues, premature failure, and costly repairs.
Common Ball Bearing Size Charts
Bearing manufacturers provide standardized size charts to help engineers and buyers select the right bearing for their needs. These charts list essential dimensions such as inner diameter (ID), outer diameter (OD), and width (W), making it easy to identify a bearing that fits a specific application.
Using these charts saves time and ensures compatibility. However, there are trade-offs to consider. While standard-size charts cover common bearing types, they may not always meet the unique demands of certain applications.
For example, high-speed or high-temperature environments may require custom bearings with special materials or tolerances not found in standard charts. Additionally, relying solely on size charts doesn’t guarantee optimal performance.
Engineers must also account for factors like load capacity, speed, and environmental conditions. If these aspects are overlooked, performance can be compromised, leading to premature wear or mechanical failure. Carefully balancing all these factors ensures the right bearing choice for maximum efficiency and longevity.
Custom and Non-Standard Bearing Sizes
In some cases, specialized machinery requires custom or non-standard bearing sizes tailored to unique performance needs. While these bearings offer superior performance for specific applications, such as high speeds or extreme environmental conditions, they come with trade-offs. Custom bearings can provide enhanced durability or precision but often come at a higher cost and longer lead time.
Moreover, sourcing non-standard bearings can be challenging, as they may not always be readily available or compatible with existing systems. Engineers must carefully consider the long-term benefits of custom designs against the additional costs and potential delays.
Despite these challenges, custom bearings are essential when standard sizes do not meet specific operational requirements. Ignoring these needs can lead to inefficiencies, increased wear, or even equipment failure. By weighing performance demands, cost, and lead time, engineers can make informed decisions that optimize the system’s overall efficiency and reliability.
Measuring Bearings: A Step-by-Step Guide
Accurately measuring ball bearings is crucial when replacing or sourcing new ones for an application. Precise measurements ensure the new bearing fits properly, maintaining system alignment and performance. Typically, three key dimensions must be measured: inner diameter (ID), outer diameter (OD), and width (W).
However, there are trade-offs when choosing the measurement method. Basic tools like calipers are affordable and easy to use, but they may lack the precision needed for high-performance applications. On the other hand, specialized equipment such as micrometers or digital calipers provide more accurate measurements but are more expensive and may require additional time for setup.
Balancing cost, time, and precision is essential. If bearings are measured incorrectly, they may not fit, leading to inefficiencies, premature wear, or even system failure. By selecting the appropriate tools and carefully following measurement steps, engineers can ensure the bearing size meets requirements, optimizing system reliability and reducing long-term costs.
Conclusion
Understanding ball bearing sizes and dimensions is essential for ensuring optimal performance, longevity, and efficiency in mechanical systems. While selecting the right size involves balancing factors like load, speed, and environmental conditions, making informed choices is crucial. Incorrect selections can lead to inefficiencies, premature wear, and costly repairs.
FAQs
1. What are the standard dimensions for ball bearings?
Standard ball bearing dimensions include the inner diameter (ID), outer diameter (OD), and width (W). These measurements help determine the bearing’s fit and function within a system. The sizes are typically standardized, but custom bearings are also available for specific needs.
2. How do I choose the right bearing size for my application?
Choosing the right bearing size involves evaluating load capacity, speed, and environmental conditions. Larger bearings support heavier loads but may generate more friction. Smaller bearings enable higher speeds but may not handle significant weight. Understanding your application’s requirements is key to making the best choice.
3. Can I use custom bearings instead of standard ones?
Yes, custom bearings are often necessary for specialized applications. While they provide enhanced performance tailored to unique needs, custom bearings come with trade-offs, such as higher costs and longer lead times. Engineers must weigh these factors carefully to ensure they meet performance requirements.
4. How do I measure a ball bearing accurately?
To measure a ball bearing, use tools such as calipers or micrometers to measure the inner diameter (ID), outer diameter (OD), and width (W). Ensure accuracy by using the right equipment for the required precision, especially in high-performance applications where precise dimensions are crucial.
5. Why is it important to follow ISO and ANSI standards for ball bearings?
ISO and ANSI standards ensure global compatibility, reliability, and interchangeability of ball bearings. Adhering to these standards helps avoid issues related to bearing performance, such as misalignment or premature failure, and ensures consistency across applications and industries.